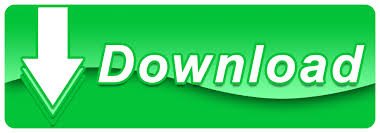
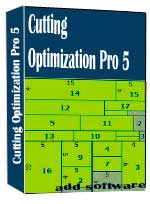
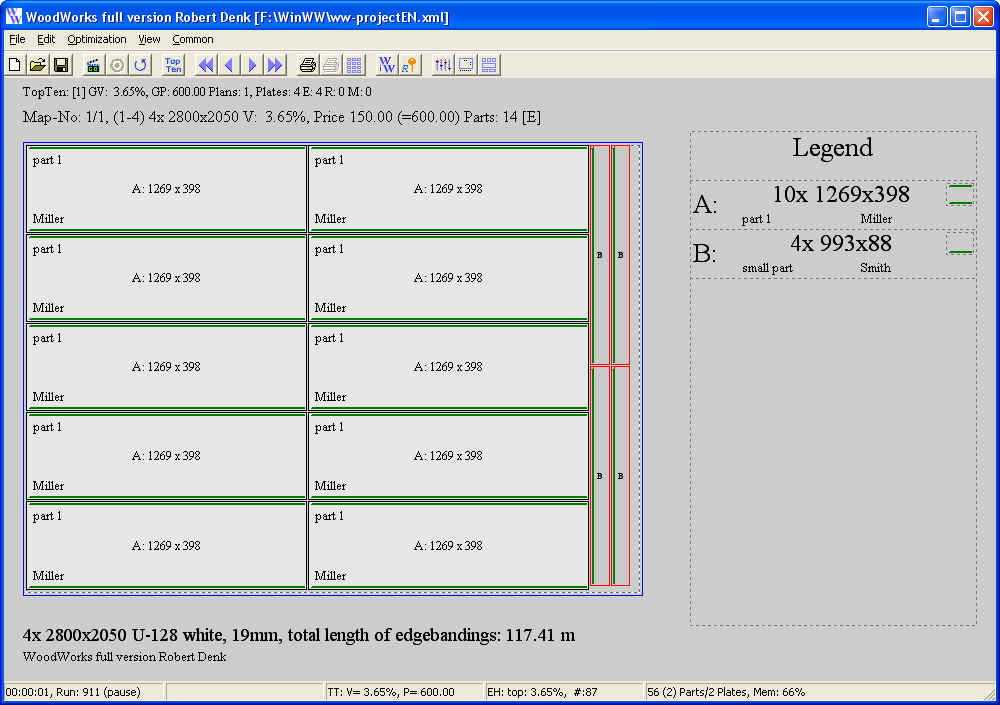
This shortens cut length and processing time and better utilizes material, since parts are nested closer to each other.Ī nest layout can employ various CLC strategies. Common-line cutting (CLC) is a technique in which a single cut is used to cut the edges of two adjacent parts at the same time. This is where another nesting strategy can help. Again, stainless is expensive, so material utilization is important. This prevents parts from being cut incorrectly and needing to be recut, a waste of both time and material.Ĭommon-line Cutting.
#Part cutting optimizer software
If the programmer nests manually, the software will signal an error when a grain restraint is violated. When nesting automatically, the software will nest these parts at only the allowed orientations. To maintain a uniform appearance of material grain on the panels, a programmer must nest parts only in orientations that run parallel to the material grain, which can be done by using a grain restraint strategy, which sets a restriction on the rotation of the parts before nesting. Since appearance is important for this appliance panel application, the laser must cut parts so that the material grain is in a consistent direction. The slug destroy strategy eliminates this risk by slicing the cutouts into small pieces during cutting so that they fall through the slats of the table. As the laser cuts small interior profiles, it can leave behind cutouts, or slugs, that can tip up and create a collision hazard for the cutting head. A laser cutting nesting strategy also must keep the process as stable as possible. This programs the laser to trace the profiles at a lower wattage before actual cutting, burning away the film. Because this stainless material has a protective film, a nest will need to incorporate the vaporize function to maintain cut quality. Appliance panels require high-quality fit and finish. Consider a typical application: a high-volume job cutting rectangular appliance panels of different sizes from 1/8-in.-thick stainless steel coated with a laser film. Laser cutting excels at producing precision parts in sheet metal and thin plate. Thankfully, fabricators can mitigate the weaknesses and accentuate the strengths, and one way to do it is to develop a smart strategy around something that’s at the heart of every cutting process in this business: nesting. Each comes with advantages and disadvantages. No cutting method is perfect in every way, of course. Cutting with a “soft tool”-be it a laser beam, plasma arc, oxyfuel flame, or waterjet-has in many ways become a defining technology of modern sheet metal and plate fabrication.
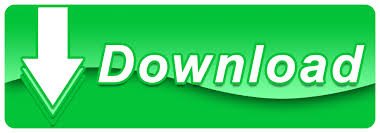